
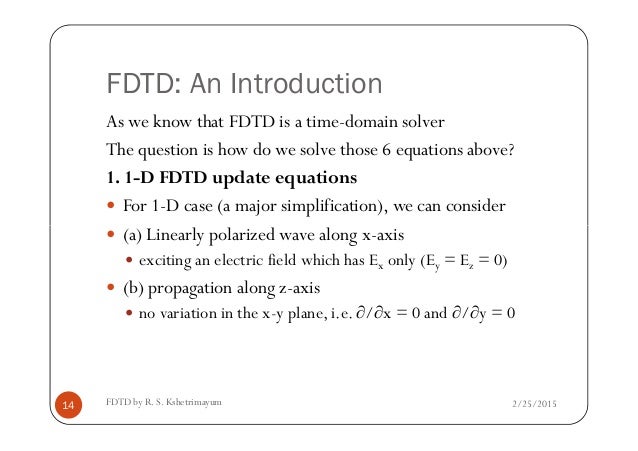
Now, go to the “Optimizations and Sweeps” window and select the optimization item named position optimization. In the “Properties” tab of the edit window, you should see the optimal grating pitch and duty cycle from the 2D optimization.Ĭlick OK to close the structure group edit window. Right click on the selected structure group and choose “Edit object” on the context menu to open the edit window. Go to the “Objects Tree” window and select the grating structure group. Instructions for running the model and discussion of key results If you are new to this example, we strongly recommend going through the preceding sections and learn about the individual steps before moving to the Advanced users already familiar with this example can proceed to this section directly. Section shows how you can use a script file to automatically run Step 3 and generate the S-parameter data. To generate the compact model of the grating coupler with CML Compiler, the S-parameter data from Step 3 can be used. S-parameter extraction: run S-parameter sweep and export the results to a data file.Ĭompact model creation: import the S-parameter data into an optical S-parameter element.Īs demonstrated in the next section, a peak coupling efficiency higher than 40% can be obtained using primarily 2-D simulations and varying the grating’s pitch, duty cycle and the fiber’s position.Ĭompact Model generation with CML Compiler Initial 2-D optimization: optimize the grating’s pitch p, duty cycle d and the fiber’s position x.įinal 3-D optimization: optimize the fiber’s position x to minimize the insertion loss. The design workflow consists of four main steps.

Because a brute force 3-D optimization with five parameters is time-consuming, a two-stage optimization is pursued here using a combination of 2-D and 3-D models and varying only three geometric parameters. These five parameters are usually optimized together to maximize the coupling efficiency at the target center wavelength. The coupling efficiency is highly sensitive to the grating’s pitch \(p\), etch length \(l_e\) and etch depth \(h_e\) as well as to the fiber’s position \(x\) and tilting angle \(\theta\). The key figure of merit (FOM) in this design is the coupling efficiency at the target wavelength. The goal of this example is to design a TE silicon on insulator (SOI) coupler with a Bragg grating fed from the top by a single-mode fiber. Understand the simulation workflow and key results It is also shown how to extract these parameters for compact model generation using the CML Compiler. The built-in particle swarm optimization tool is used to maximize the coupling efficiency, and a compact model in INTERCONNECT is created using the component S-parameters. Design a grating coupler connecting a single-mode fiber on the surface of a photonic chip to an integrated waveguide.
